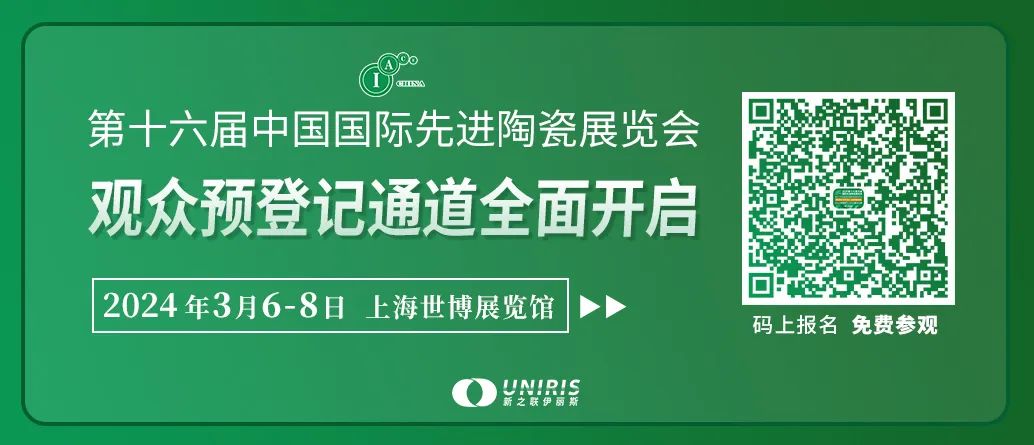
随着军用载具所受威胁的不断升级,对于驾驶舱的防护要求也在增加。传统以防弹玻璃为主的透明装甲已难以满足使用要求。更轻更薄的陶瓷基透明装甲正在逐渐成为主流选择。与其他防弹装甲相似,透明防弹装甲的主要研究方向包括:寻找性能更优的材料用于装甲组件;通过实验或计算机模拟对结构设计与弹道实验进行指导;更加深入地了解装甲材料所需的主要性能、系统整体性能以及整个系统各组件之间的相互影响。依据这一思路,本文首先简要综述了陶瓷透明防弹装甲研究较多的三种迎弹面陶瓷材料的优缺点、制备工艺以及各自的发展及应用水平,三种陶瓷中蓝宝石的静力学参数最优,而实际防弹效果则以多晶陶瓷更好,导致这一现象的原因主要是两类陶瓷碎裂模式的不同产生的弹丸-陶瓷相互作用效果的差异;然后对多晶陶瓷、单晶、玻璃三种类型材料高应变率下的裂纹扩展特性和防弹性能进行了讨论,高应变速率下材料裂纹扩展特性对冲击能量/速率是敏感的,多晶陶瓷是沿晶断裂和穿晶断裂的复合扩展方式,蓝宝石高能冲击下裂纹扩展特征类似多晶陶瓷,临界能量以下则以沿特定晶面的解理断裂为主;最后对透明防弹装甲各功能层的选材标准和结构设计原则进行了总结与展望,迎弹面优选高杨氏模量、高硬度的细晶粒多晶陶瓷材料,中间层选用具有良好的断裂韧度、高弯曲刚度以及将破碎控制在较小范围的能力的材料,背弹面要求材料具有一定的延展性和低密度的特点。各层之间需相互配合才能实现透明陶瓷装甲防弹效能的最大化。随着武器装备的不断发展,对载具防护的要求也在日益增强。针对军用直升机和地面载具驾驶舱的保护材料,要在兼具透明性的前提下,大幅度提升应对机(车)身正面和侧面的抗弹击伤亡能力,有效提高载具被击中后的人员生存概率,保证人员安全,满足军用载具高生存力设计要求。在过去数十年,防弹玻璃因为成本低、易于批量生产、透光度高等特点,一直是透明防弹装甲的主要材料。据报道,2015年度的全球防弹玻璃产值为23.96亿美元,预计到2021年,该数字将达到约40亿美元。然而,伴随着载具轻量化、集约化的要求,对透明装甲材料的要求也不断提高。如果以传统防弹玻璃作为主材,要抵御大口径步枪子弹的攻击,就要大幅度增加装甲厚度。这会造成一系列负面影响:增加载具自重、降低机动性、压缩舱内空间、损失光学性能。美军曾为高机动性多用途轮式车辆(HHMMWV,汉姆威)额外配装“装甲生存工具包”,其中透明装甲就占到车辆总重的30%以上,然而仅覆盖了车身15%的外部面积,所以透明装甲减重对于实现载具轻量化至关重要。因此,开展高抗弹性轻质陶瓷基透明装甲研究是十分必要的。新型透明防弹装甲结构由三个功能层组成:使弹丸钝化、损伤、碎裂的迎弹面层;能量吸收、止裂、缓解热膨胀错配的中间层;防碎片飞溅的背弹面层。此外还有各层之间的黏结层(用于连接系统并提供多次撞击阻力),典型结构如图1所示。迎弹面通常由玻璃、玻璃陶瓷或透明陶瓷制成,中间层由玻璃或聚甲基丙烯酸甲酯(PMMA)构成,而背弹面通常选择聚碳酸酯(PC)。
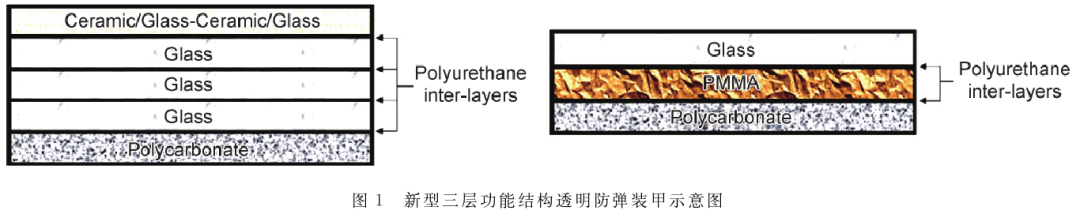
目前透明装甲的研究和设计工作,更多仍是基于经验方法。对于透明装甲材料的变形、破坏行为及各功能层之间的相互作用和集成机理仍缺少深入的认识。因此本文对陶瓷基透明装甲相关研究进行综述,重点介绍目前作为迎弹面的三种透明陶瓷的优缺点及研究进展,透明装甲破坏行为分析研究,透明装甲不同功能层所起到的作用及设计准则。
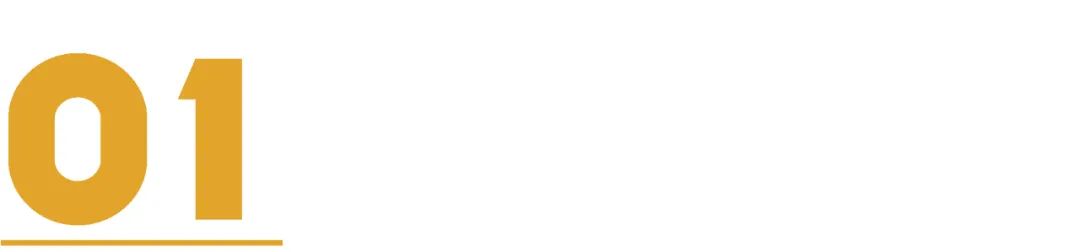
迎弹面陶瓷材料研究进展
迎弹面是整个透明防弹装甲系统的核心。陶瓷材料由于更高的硬度和抗压强度,成为目前最为先进的透明装甲材料,通常用于抵抗最致命威胁的场景。当迎弹面层使用单晶蓝宝石,多晶ALON或镁铝尖晶石等透明陶瓷材料时,相比于玻璃材料可以减重减薄达30%~60%。
蓝宝石材料是目前应用最为普遍的透明装甲用陶瓷材料,最主要的原因在于三种陶瓷材料中蓝宝石的技术研究更为成熟,具有广泛的商业化产品选择。目前大多数尖晶石透明陶瓷的核心问题是难以获得高质量的原料粉体,商业粉末又存在不够纯净或颗粒尺寸过大/过细等问题,相较之下,蓝宝石因其所需单晶制备技术可避免原料因素影响。此外,蓝宝石的静态硬度、抗弯强度和杨氏模量均高于多晶镁铝尖晶石和AlON,具有高化学抗性,广泛的可用性等特点。但是,由于蓝宝石需要较高的加工温度以及繁琐的工艺,使得其制备成本很高。单晶泡生法(KY)和直拉法(CZ)制得的蓝宝石为了满足光学需求均需要大量的后处理,由此导致原料利用率低的问题;导模法(EFG)可以实现单曲平板制备,提高了原料利用率,但是需要大量钨钼原件,成本高昂,批次稳定性不高。此外,由于单晶生长内应力大,易发生不规则脆性开裂和解理裂纹,影响后期层合及装配。尽管存在着以上提到的这些问题,但是目前蓝宝石陶瓷依然是透明装甲的主流材料。不过随着技术的深入,通过晶粒纳米化、晶粒定向生长、固态晶粒生长法等手段,多晶Al₂O₃的光学性能也在不断提高。在不久的将来有希望获得具有与单晶蓝宝石相当光学与力学性能的多晶Al₂O₃材料。多晶镁铝尖晶石是MgO-Al₂O₃系统中唯一中间化合物。多晶镁铝尖晶石因为其光学性能、高速冲击抗力和生产成本之间的平衡,是最具前途的装甲迎弹面材料之一。相比于蓝宝石及AlON,多晶镁铝尖晶石在中红外波段具有更高的透光率和红外吸收边,这对于搭载有红外探测设备的载具,具有更好的适用性;同时具有与另外两种陶瓷材料相似的抗高速冲击性能,但杨氏模量和硬度略低。目前,多晶镁铝尖晶石难以通过常规烧结手段达到透明所需的理论致密度,这是因为它对粉末尺寸、团聚体、杂质和助剂都十分敏感。多晶镁铝尖晶石的原料粉末可以通过机械合金化、固相烧结、溶胶-凝胶、水热法、共沉淀和化学气相沉积等多种方式获得,不同合成方法决定了原料粉体的性能。镁铝尖晶石粉末的化学计量比、杂质、粒径和团聚体的缺陷无法通过调整工艺参数来改善。杂质不仅影响镁铝尖晶石的光学性能,同时会改变界面能和晶界迁移速率,进而影响微观结构、硬度以及高速冲击抗力。适量LiF烧结助剂可减少透明镁铝尖晶石中的杂质,但是会造成材料脆化,断裂形式从穿晶断裂转变为沿晶断裂,降低材料的高速冲击抗力。多晶镁铝尖晶石的烧结是一个亟须解决的问题,这是因为:Mg或MgO的挥发导致产生化学计量比变化(MgO的蒸气压是Al₂O₃的103倍)及梯度;晶粒具有较高粗化倾向;低氧晶格扩散速率要求较高烧结温度。目前商用透明多晶镁铝尖晶石是通过无压烧结/热等静压或热压烧结/热等静压烧结的,这些工艺制造成本依旧高昂,几乎难以生产大型板材。热压烧结相比于无压烧结,提高了烧结驱动力,降低了裂纹、翘曲等风险。无压或热压后的热等静压处理是必须的,这一过程可以进一步降低孔隙率而提高透明性。放电等离子烧结(SPS)是近些年研究的热点。SPS方法可以显著降低烧结所需温度,并提高产品力学和光学性能。然而,目前采用SPS工艺同样无法实现大尺寸板材的制备,尺寸增加后,SPS存在的温度梯度会导致样品加热不均,导致透光率损失等问题。AlON是一种缺陷立方尖晶石结构的多晶透明陶瓷,化学式可表示为Al(64+x)/3O32-xNx(2≤x≤5)。ALON的合成方法有多种,如氧化铝的碳热氮化、氧化铝和氮化铝的等离子熔炼或微波合成、氧化铝与氮化硼的反应烧结。AlON的烧结方法也主要是反应烧结、无压烧结、热压和热等静压等传统烧结工艺。因为工艺简便、原料易得、产品污染小等优势,目前最广泛的制备手段是氧化铝和氮化铝之间的反应。20世纪70年代美国陆军实验室和Raytheon公司开展了透明ALON的研究,使得Raytheon在20世纪末成为唯一可以生产高质量ALON陶瓷的公司。而后,Surmet公司获得了技术转让,并通过无压烧结和热等静压烧结实现了批量化大尺寸AlON陶瓷的生产及工程化应用,目前已实现约0.74m2的、高光学质量AlON透明陶瓷,如图2所示,并可以通过无缝拼接技术实现更大尺寸样品的制备。
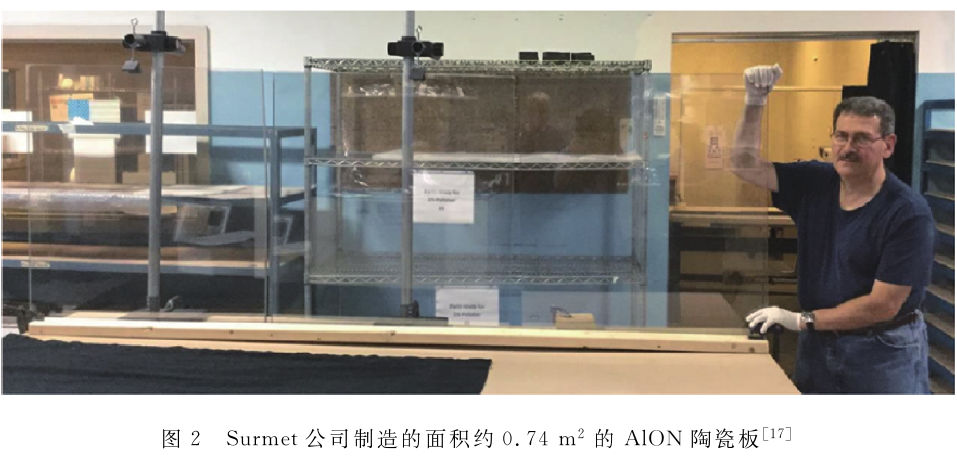
虽然在过去几十年,制备手段获得长足进步,但是在大规模制备过程中尚存在一些困难,首先是干燥过程会出现收缩现象,在生坯内部生成裂纹;其次,大尺寸AlON的烧结也会因温度不均匀产生微观结构的不均匀,进而导致应力双折射现象。三种陶瓷材料的力学性能如表1所示。蓝宝石的静态力学性能除抗压强度外,均优于另外两种陶瓷材料。甚至是一些动态特性,例如Hugoniot弹性极限(HEL)等,蓝宝石同样优于其他材料。然而许多研究发现,在实际的防弹测试中,结果是镁铝尖晶石和ALON等多晶陶瓷的防弹性能更高。例如Swab等比较了V50(发生50%完全穿透的概率时的速率)与透明装甲面密度之间的关系,结果显示AlON和镁铝尖晶石的V0相对于蓝宝石分别提高了约5%和10%。Patterson等通过对每种材料V50除以相同面积材料质量的结果也得出了相类似的结论,多晶陶瓷的性能优于蓝宝石和玻璃。
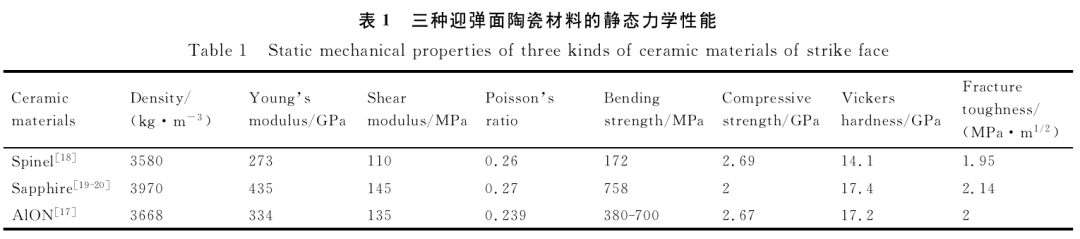
许多研究从这些材料的动态响应、冲击响应和断裂行为三个角度,为这种防弹性能与力学参数之间的差异做出了解释Haney等采用动态和静态压痕法分别分析了蓝宝石和镁铝尖晶石的裂纹扩展特性,结果显示无论动态还是静态压痕,蓝宝石压痕裂纹扩展都是沿着特定晶体学平面传播,而与压痕对角线方向无关。相比之下,镁铝尖晶石的压痕扩展行为就受加载速率影响较大。镁铝尖晶石在静态压痕实验中,压痕裂纹起初沿对角线方向延伸,遇到晶界后则偏离初始轨迹沿晶界扩展;而在动态压痕实验时,裂纹出现了明显的穿晶断裂现象。采用冲击实验验证这两种相异的裂纹扩展模式对防弹性能的影响,实验使用直径4.76mm钢球以280m/s的速率撞击尖晶石和蓝宝石棒状样品。尖晶石产生混合型裂纹,可以将裂纹区分为两个不同区域,接近撞击点区域,发生高度碎裂,在这一区域弹丸能量通过穿晶、沿晶断裂,碎裂物质的膨胀,粉碎物质喷射动能的方式耗散。而在远离撞击点的区域,则主要是以沿晶断裂为主,结构完整性也得以保留。相比之下蓝宝石的断裂则主要是沿特定晶体学平面的定向长裂纹形式出现,并形成了等间隔的c轴取向的严重碎裂带。这就造成蓝宝石出现毫米尺寸的大块碎片,结构完整性遭到严重破坏。同时冲击点附近喷射物质非常少。撞击尖晶石的钢球受到喷射物的冲击,不仅使钢球减速,同时冲蚀钢球,钢球表面具有明显塑性变形、断裂、冲蚀痕迹。而蓝宝石没有形成这种细碎喷射物,大碎片被弹丸推开,因此表面只发生塑性变形和断裂,缺少冲蚀痕迹。通过对能量耗散形式的分析,将尖晶石相较于蓝宝石更优的防弹性能归因于以下3点:(1)尖晶石的多晶性质导致更高的单位体积断裂面密度,而蓝宝石沿晶体学平面形成长裂纹断裂密度较低。尖晶石断裂产生的能量耗散更大;(2)尖晶石由于材料破碎流动而耗散的能量要高出蓝宝石一个数量级。细化的碎片可以有效减速和冲蚀入射的子弹,从而显著减少弹丸侵彻靶板的动能。另一方面,蓝宝石沿特定晶面的断裂,大碎片被从弹丸路径中推开,无法阻止子弹进入靶板更深的地方;(3)蓝宝石结构完整性损失更大。虽然碎片运动是一种有效的能量耗散手段,但是蓝宝石的大块碎片无法阻碍进一步的侵彻,因此也会造成严重的危害。
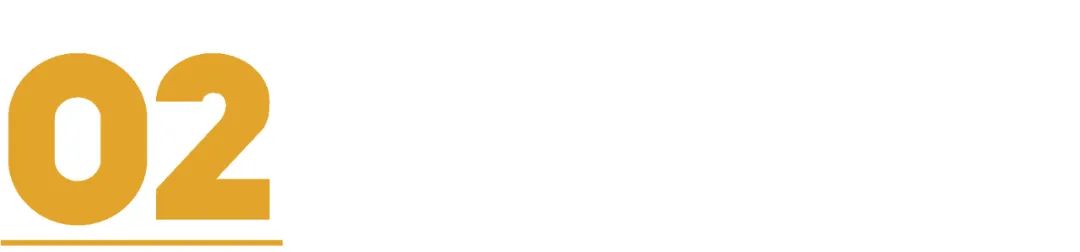
透明装甲破坏行为分析
依据1.4节中的讨论,弹击动态加载情况下,材料力学参数和实际防弹性能存在不一致的现象;此外也通过冲击实验理解了蓝宝石作为迎弹面材料防弹性能不如多晶陶瓷的原因。而在本节中,将继续通过其他研究者对透明装甲破坏行为的研究,进一步理解不同材料、不同结构装甲在高应变速率下的裂纹形核、拓展,缺陷影响,和材料失效情况等。
高应变速率的动态测试(102~104s-1)相比于准静态情况(10-3~10-2s-1)下材料失效行为会有较大差异。准静态情况下,材料一般是从最主要缺陷失效,而且应变特征较为单一。而在动态加载情况下,会同时出现拉、压、弯等多种应力形式,应力体积也是准静态下的数百到数千倍,从而激活了更大的缺陷分布、微观结构不均匀性和其他应力集中区域而发生失效。冲击发生后,一般会在材料体内出现三类应力波:分别为面波(瑞利波)、纵波(压缩波)和剪切波。在弹击这种法向载荷的情况下,能量分布大致是瑞利波67%,剪切波26%,压缩波7%。尽管瑞利波能量较高,但除了具有明显表面缺陷的材料,一般导致材料失效的关键波仍是压缩波和剪切波。具有更大能量的剪切波,可以使得裂纹生长、传播并聚集成损伤前沿。McCauley等针对AlON、蓝宝石和层合玻璃板进行了边缘冲击实验,通过透射光的阴影图和反射偏振光记录裂纹扩展和应力波传播。AlON陶瓷遵循多晶陶瓷受冲击时的典型裂纹扩展模式,即有一个半圆形的主裂纹区,这一区域的裂纹未分化,以连贯的大裂纹为主。而在主裂纹区前有一些分立的圆形阴影区域,这是在应力波作用下的裂纹中心,即裂纹形核发生的区域。即使材料是透明的,但是不代表没有任何的体缺陷,一些应力集中区域,都会成为裂纹形成和拓展的应力集中源。AlON陶瓷遭受高速率碰撞和低速率碰撞之间没有明显的损伤形态差异。一个可能的解释是AlON的非弹性或塑性变形机制减缓了裂纹/损伤的拓展。断裂机制除了沿晶裂纹外,还有明显的穿晶解理机制在发挥作用。通过对AlON内的应力波进行计算机计算模拟,结果表明,实验中观察到的损伤区域基本上对应于由于波传播而发生剪切的区域,压缩波可以从现有缺陷(应力强度/浓度区域)激活裂纹,这会把传递的压力增加到临界水平,然后随着横波的传播,裂纹将开始广泛生长。针对上述实验研究结果,Zhang等采用计算机模拟还原相似参数下钢柱弹丸冲击AlON多晶陶瓷板的应变能密度和损伤演变。模拟结果发现损伤发展有两个阶段:第一阶段是快速移动的损伤前沿导致的大规模碎裂,而进入第二阶段则过渡为从损伤前沿萌生的移动相对缓慢的局部裂纹扩展。平板的厚度中心和边缘的损伤情况不同,损伤首先发生在表面上,然后才到达中心层。与外表面切片层相比,中心层的损伤较少。这一差异会在厚度更大、晶粒更多的样品中愈发明显。使用改进的Kolsky杆和高速相机记录ALON在单轴和高应变速率压缩情况下的动态失效,加载速率155MPa/μs。考察应用单轴约束状态和无约束状态的应力变化,有约束样品相对于无约束样品最大应力从3.5GPa上升到4.5GPa,压缩应力-时间曲线斜率出现了明显变化,表明转变为塑性机制。边缘约束抑制了裂纹的形成,增加了最大承载应力,允许纳/微米解理激活,使得变形机制变为类似塑性形变的非弹性变形机制。在1.4小节中讨论了蓝宝石陶瓷在动态过程中解理的重要性。在本节中通过更可控的边缘冲击实验来进一步理解蓝宝石的断裂机理。图3(a)是39.1g的钢球弹丸撞击蓝宝石方向1(冲击平行于a轴,正对镜头平面为(0001)面,如图4(b)所示)后不同时刻的高速摄像照片。通过裂纹演化照片可以看到第一个裂纹,在撞击后立即出现,可能沿着棱柱状解理面(m面),在试样中切出一个大约120°角的圆锥体(裂纹A,B)。2.7μs后,可见第三条主断裂,沿冲击方向(裂纹C)直线扩展。大约8μs后,裂纹以约60°的角度从锥形裂纹上分叉,并沿冲击方向生长。裂纹C也以约55°的角度从中心断裂处分叉。图3(c)是采用54g柱状弹丸对样品进行冲击后不同时刻的高速摄像照片,撞击后1.2μs的照片显示,裂纹的形成是从弹丸边缘开始的,在此处剪切应力占主导地位。3μs后,在弹丸前方形成了一个密集的断裂带,形成了近半圆形。因为钢柱弹丸的冲击能量更高,就造成了与钢球模型冲击(裂纹沿晶体学方向/解理面拓展)的明显不同,有效解理面无法控制损伤前沿形貌,更加接近多晶ALON的断口形貌。蓝宝石主要的解理面有c面(0001)基面;r面(1012)菱形面和m面(1010)棱柱面。三个面的KIC和解理能分别如下:c面4.54MPa·m1/2和21.54J/m²;r面2.38MPa·m1/2和6.45J/m²;m面3.14MPa·m1/2和11.43J/m²。即裂纹会更易在r面扩展,然后是m面,沿着c面扩展最为困难。图4是采用不同速率球形弹丸对整体玻璃冲击后不同时刻的正面高速照片。图4(a)是以100m/s弹丸速率为代表的弹丸未侵彻玻璃(100~500m/s)的损伤特征,高度离散断裂是主要的失效模式:冲击后形成断裂锥,径向裂纹延伸至玻璃片边缘。
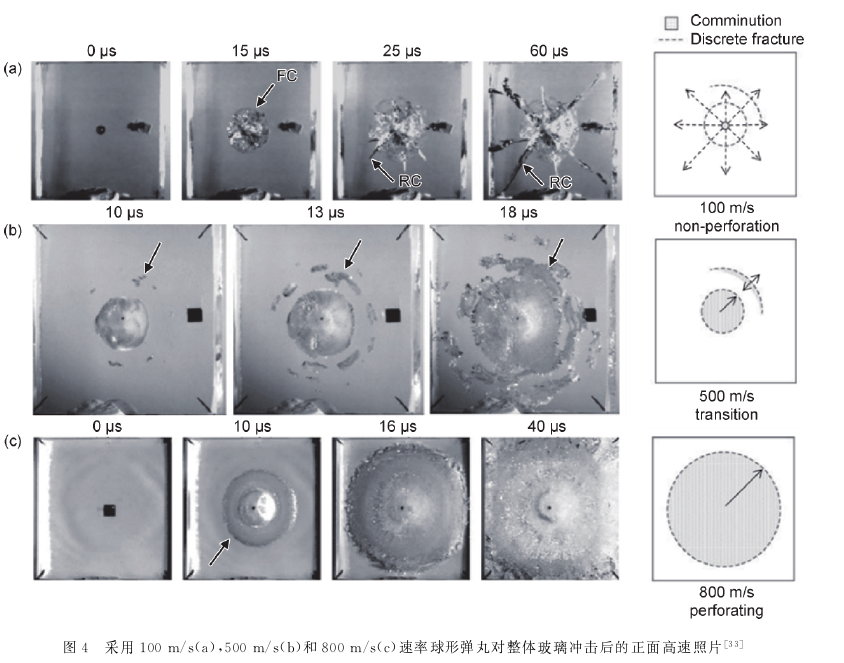
图4(b)是以500m/s弹丸速率为代表的未侵彻向侵彻过渡的中间速率(500~550m/s)损伤特征,同时存在粉碎和离散断裂,离散断裂(裂纹中心)领先于主损伤前沿,从而引发进一步损伤,并最终与主损伤区结合,这一损伤形貌也与多晶陶瓷边缘冲击实验结果相似。图4(c)是以800m/s弹丸速率为代表的侵彻速率(550~800m/s)的损伤特征,通过大量碎裂失效,并发展为单一损伤前沿。针对玻璃材料的边缘冲击实验显示,与多晶材料相似,玻璃材料同样是在连贯的主损伤区前有若干分离的裂纹中心区域。在对层合玻璃进行边缘冲击实验时发现,压缩应力波会从每层玻璃板的后边缘以拉伸波形式反射。当第一层玻璃损坏,且第二层玻璃后边缘应力波已经发生反射,则第二层玻璃的损伤可能会由拉伸波引起,破坏发生在第二层玻璃的后边缘。从以上结果应该注意到,防弹装甲的第二层同样会承受很强的应力波作用而极易发生损坏,因此在透明装甲的设计过程中除考虑中间层的能量吸收作用外,也应该考虑该层的强度要求。
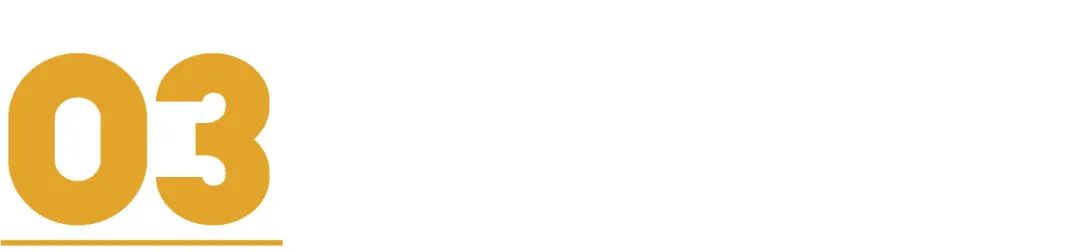
陶瓷基透明装甲材料与结构设计
正如蓝宝石优秀的力学性能无法代表最好的防弹性能,透明装甲作为一个功能性的系统,并不是每种组成材料的性能的简单堆砌,还与系统中各组件之间也会发生相互作用类型以及相互间影响程度有关。一个直观的例子可以证明此观点,在刚性背底支撑(钢)的情况下,材料的防弹质量效率与迎弹面材料的硬度存在正相关关系;然而当采用较软背底支撑(铝)时,装甲的防弹性能与硬度之间的关联性消失。本工作将探讨各功能层的主要作用、影响材料选用的因素以及装甲结构的优化。通常将弹丸及迎弹面材料的相互作用分为两个不同的阶段———停留阶段及侵彻阶段。停留阶段是指弹丸撞击在迎弹面上,而未发生穿入,从弹丸失效的角度来看,这一阶段的最主要目的是延长弹丸停留时间,从而确保弹丸尖端最大程度地钝化、碎裂。为了实现这一目的,则需要材料具有较高的刚度(高杨氏模量),以及高非弹性变形阻力(可以通过细化晶粒实现)。而侵彻阶段,则是弹丸进入迎弹面材料中,主要的弹丸失效方式变为塑性变形以及陶瓷碎片的反向喷射对弹丸的冲蚀。因此这一阶段,获得相对大尺寸的高硬度碎片,可以有效增加冲蚀效果(大尺寸碎片要求可以有效冲蚀弹丸,而非1.4节中无喷射效果的蓝宝石宏观碎片)。而为了获得较大的碎片尺寸,要求迎弹面材料有较小的晶粒尺寸,较高的杨氏模量从而促进少量裂纹生长而非大量小裂纹形核,且迎弹面材料发生的弯曲尽可能小,此外,对透明装甲外加侧边及厚度方向上的约束,也可以有效增加碎片尺寸。综上所述,最优的迎弹面材料应该是具有高杨氏模量、高硬度的细晶粒多晶陶瓷材料,即ALON和镁铝尖晶石陶瓷材料。针对晶粒尺寸的影响,需要单独说明的是有实验结果表明不同晶粒尺寸的镁铝尖晶石材料,细晶粒陶瓷板的V50相对于粗晶粒样品高出18m/s,这是非常显著的差异,对防弹性能有积极影响;然而对于已经发生侵彻阶段的靶材,二次侵彻时粗晶材料在停留后的侵彻速率应该比细晶材料慢,造成细晶粒材料后续侵彻深度更大,由此可见,微观结构对防弹性能的影响仍然是值得进一步研究的。而在迎弹面层结构设计方面,坚固的侧边约束和厚度方面上夹紧的装甲框架,不仅可以增加碎片尺寸,同时增加非弹性变形机制(如2.1节所述),在弹丸停留阶段提高防弹性能,还可以减缓裂纹扩展。采用坚固的中间层材料可以提供厚度方向上的空间约束。在不影响光学功能的前提下在迎弹面前附加坚硬覆盖物可进一步增加空间约束,且与中间层的配合下在迎弹面的压缩中产生预应力,可以进一步提高防弹性能。最后,单层迎弹面层防弹性能优于多层层合的迎弹面。在弹丸通过迎弹面后,已经发生明显的减速,同时弹头已经发生钝化或碎裂,因此在中间层最主要的特征是伴随着中间层材料碎裂的能量吸收。因此具有良好的断裂韧度以及将破碎控制在较小范围是中间层材料的关键要求。如前所述,坚硬的背衬支撑也可以提高迎弹面层的防弹效率,从而使陶瓷材料的超高硬度得以充分利用,这就需要中间层材料具备高弯曲刚度,这需要高杨氏模量和增加中间层厚度来实现。从这一角度看PMMA(有机玻璃)、玻璃陶瓷和玻璃是理想的中间层材料。而从对弹丸动能吸收的角度看,具有断裂韧度(单位碎片表面积吸收的能力)和小尺寸碎片(即碎片总表面积)的良好组合至关重要,将损伤限制在弹击处周围一个狭窄的区域内同样非常关键。因此虽然PC(聚碳酸酯)材料的断裂韧度更高,但是会产生大量更细碎碎片的PMMA和玻璃更加胜任中间层材料的要求。结构设计方面,为了提供迎弹面坚硬支撑,需要提高弯曲刚度,除了通过材料自身性能来实现外,还可以通过该层提供一个较小的向外曲率来实现。而采用单层中间层结构可以更好地吸收弹丸能量,并增强抗多次打击防弹能力。背弹面材料主要是阻碍弹丸及迎弹面和中间层碎片进入载具中,并保证自身不脱落,极少发挥实际防弹效应。因此该层要求材料具有一定的延展性,而从轻量化角度来看,该层倾向于使用密度较低材料。从以上角度考虑,PC和PU(聚氨酯)材料是较好选择。实验结果表明,PC板材的极限防侵彻速率为125~130m/s,所以为了确保透明装甲的防弹有效,应保证通过迎弹面层和中间层将入射弹丸降低到该速率以下。而从结构角度来看,多层背弹面层的碎片抑制能力更好。此外,应使用较厚的夹层将该层与中间层机械隔离。
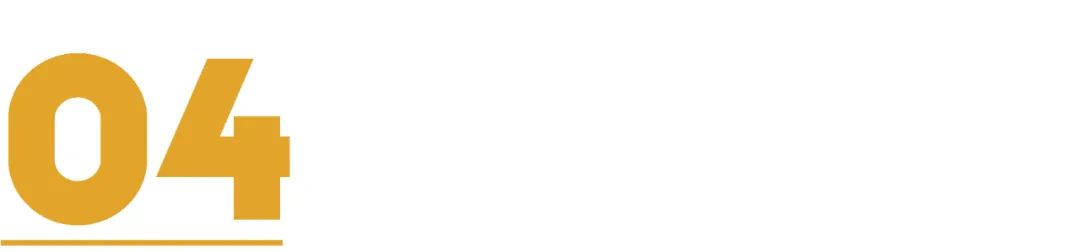
机遇与挑战
近些年来,计算机模拟技术的发展也为防弹透明装甲设计提供了更有效的途径。目前一种方法是基于理论模型分析,主要对材料力学模型进行简化分析,从而求解给定条件下的侵彻理论公式。Chen等从能量耗散的角度建立剩余侵彻深度的理论计算模型,该模型通过预知弹体质量,弹体初速,弹体材料动态屈服强度,弹体横截面积,弹体材料密度,靶材动态屈服强度等数值计算弹头剩余质量和穿出迎弹面层后的剩余速率。然而理论模型分析方法依赖基于经验的“系数”或“因子”,也无法充分表现侵彻的物理过程。所以数值模拟计算是分析侵彻过程的主流方法,这类方法基于计算模拟软件,可以通过图形界面快速直观地给出弹丸侵彻过程,相对于理论模型分析研究的内容更加丰富。Xiao等采用光滑粒子流体动力学方法(SPH)模拟了纯钨弹丸冲击氧化铝靶材过程中的弹丸和靶材碎裂,模拟结果对靶材的反向喷射物及背面凸起的形成和运动、弹丸的变形与冲蚀过程进行了较为准确地再现,此外对弹丸剩余速率和残余质量的预测精度较高。Sun等模拟了长杆弹丸冲击有预应力约束的陶瓷靶的情形,模拟中设定了多种预应力加载情况(径向、轴向和流体静力的以及无预应力),结果显示提高约束预应力可明显提高陶瓷复合装甲的抗侵彻能力,这与2.1节中的实验结果相一致。王维占等对侵彻陶瓷复合结构靶材过程中制式穿燃弹的质量变化、不同侵彻角度下弹道极限和破坏形态等参数进行了模拟计算,结果与实际实验结果相一致,这类研究会对具体弹型有要求的防弹透明装甲的厚度和结构设计有重要的指导作用。与此同时,也应该意识到陶瓷基透明防弹装甲仍有许多难题需要我们挑战。最首要的问题是当前单块透明陶瓷板材的尺寸基本无法满足实际使用要求,这就需要对透明陶瓷进行拼接。截止目前,应用比较广泛的方法有玻璃粘接、活泼金属钎焊、瞬间液相连接、钼锰法等。活泼金属钎焊在工业上应用最为广泛,主要采用Ti或其他活泼金属(例如Zr,Nb,Cr,Y等),这些金属与蓝宝石等润湿性良好,在800~900℃数分钟即可完成钎焊,优点是连接紧密,缺点是热膨胀系数匹配较差在接缝处产生残余应力,工艺要求超高真空环境,所以成本较高。瞬间液相连接方法所需温度低,因为连接层采用多层结构,表现出优异的耐高温性能;然而需要长时间保持才可消除连接层缺陷,因此生产周期长、工艺成本高,这严重限制了瞬间液相连接技术的应用。钼锰法主要包含Al₂O₃陶瓷金属化和使用合适钎焊合金将金属化的Al₂O₃粘接,这一工艺需要高温、生产成本高,且金属化层内往往有气孔、微裂纹缺陷等。玻璃粘接方法是将多种玻璃(MgO,CaO,SiO₂,TiO₂,Al₂O₃等)形成物进行混合,作为填充材料进行烧结,该方法所需温度较低,反应可以在非真空、非保护性气氛下进行,也是仅有的能保持接缝透明的方法,是透明陶瓷装甲焊接的最佳选择,例如使用BaTiAl6O₁₂激光焊接蓝宝石,粘接完成后仍可保持可见光波段80%的透光率。陶瓷基透明防弹装甲面临的第二个问题是无法做出复杂形状装甲,绝大多数装甲仍是平板状,因此限制了载具的设计。多晶陶瓷制备技术的进步将一定程度上解决这一难题,不过仍有曲面陶瓷与玻璃及有机材料形状匹配,边缘设计与装配等一系列问题有待解决。因此,陶瓷基透明防弹装甲依然有极大的提升潜力。
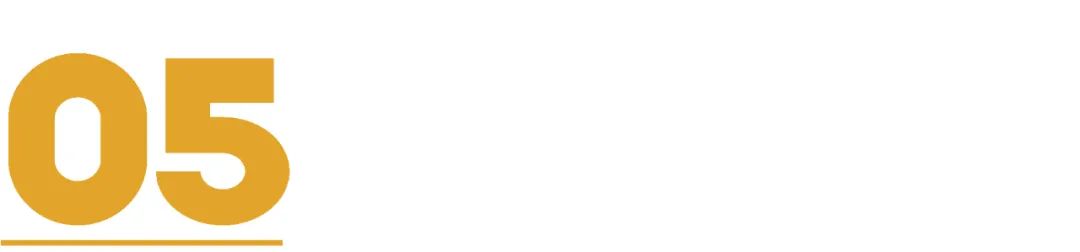
结束语
陶瓷基透明装甲相对于传统防弹玻璃可以在减重减薄达30%~60%的前提下,实现更好的防弹性能。现有针对陶瓷基透明装甲的研究主要集中在三个方面:寻找性能更优的材料用于装甲组件;通过实验或计算机模拟对实际弹道实验进行指导;更加深入地了解装甲材料所需的主要性能、系统整体性能以及系统各组件之间的相互影响。本文依循这一逻辑思路,引述了一些具有代表性的陶瓷基透明装甲的研究工作,得到的结论如下:(1)蓝宝石材料是目前工艺最为成熟的迎弹面陶瓷材料,然而其制造成本高昂,批次稳定性较差。多晶陶瓷材料,例如镁铝尖晶石和AlON,则具备生产更大尺寸样品的可能性。目前制约其发展的主要是难以获得高质量原料粉体的制备和烧结工艺问题。现今已可生产面积0.5m2以上样品,具备实际应用的价值。从单纯力学性能数据上看,蓝宝石材料明显优于多晶陶瓷材料。然而实际的抗弹击性能则与之相反,多晶陶瓷会在高加载率情况下产生更高的单位体积断裂面密度,从而产生更高能量耗散,同时产生更多细碎碎片反向冲蚀弹丸并显著减少弹丸进入靶材的动能。多晶陶瓷还可以在弹击情况下保持更好的结构完整性。(2)多晶陶瓷受到动态冲击,会产生一个近似弧形的主损伤区,在主损伤区前端会有缺陷产生的裂纹中心,裂纹从这些裂纹中心形核,在应力突破临界条件后,裂纹开始生长,融入主损伤区。多晶陶瓷的断裂模式为穿晶断裂和沿晶断裂的复合断裂模式。边缘增加约束可以增强塑性机制,抑制了裂纹的形成,增加最大承载应力。蓝宝石主要为特定晶面控制的解理断裂,当冲击能量过高,则裂纹形貌与多晶陶瓷相似,当裂纹延伸至材料内部,应力降低,裂纹开始沿特定晶面生长。玻璃材料损伤形貌也对冲击能量/速率敏感,从层合玻璃结果看,应力波除造成迎弹面层明显损伤外,第二损伤区通常出现在中间层(第二层)的背部位置。(3)迎弹面材料应该选择具有高杨氏模量、高硬度的细晶粒多晶陶瓷材料。坚固的侧边约束和厚度方面上夹紧的装甲框架、刚性的中间层可以进一步增强迎弹面层防弹性能,中间层主要承担能量吸收的作用。因此具有良好的断裂韧度、高弯曲刚度以及将破碎控制在较小范围的能力是中间层材料的关键要求。为了提供迎弹面坚硬支撑,需要提高弯曲刚度,这可以通过该层提供一个较小的向外曲率来实现。背弹面层要求材料具有一定的延展性,该层倾向于使用密度较低材料。结构角度来看,多层背弹面层的碎片抑制能力更好,该层与中间层之间应该用较厚的夹层进行机械隔离。透明装甲作为一个功能性的系统,需要各组件间相互协调才能发挥每种材料的最佳性能。作者:刘家希1,2,石晓东3,姜良宝1,2,李晓宇1,2,王敏博1,2,颜悦1,2(1中国航发北京航空材料研究院;2北京市先进运载系统结构透明件工程技术研究中心;3新时代工程咨询有限公司)
声 明:文章内容来源于特种防护圈。仅作分享,不代表本号立场,如有侵权,请联系小编删除,谢谢!
CopySearchShareFavoriteUnderline
people underline